钢的热处理工艺-时间-温度-转变曲线- 气体渗碳中时间和温度与渗碳的关系

图 2 时间-温度-转变曲线
质量的影响– 钢的质量对马氏体的形成有影响。可以看出,即使是尺寸相对较小的样品,散热速率也不均匀。热量总是以比内部药水更快的速度从表面层排出。在给定的冷却介质中,表面和内部的冷却速度随着样品尺寸的增加而降低,超过临界冷却速度的可能性变得越来越小。为了克服这个问题,钢需要在具有非常高热量去除率的介质中淬火,例如冰盐水,但即便如此,许多钢对响应完全硬化的更大尺寸有物理限制,无论的淬火介质。
碳的影响——普通碳钢和低合金钢中的碳含量会影响 Ms 转变温度。随着碳含量的增加,Ms 温度降低(图 3)。
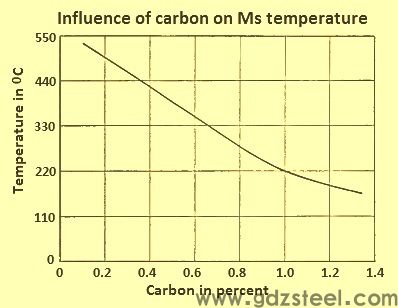
图 3 碳对 Ms 温度的影响
回火
回火(有时称为拉伸)是将硬化(马氏体)或正火钢重新加热到低于 A1 温度的某个温度的过程。除了一些易受回火脆性影响的钢外,冷却速度并不重要。随着回火温度的升高,淬硬钢的马氏体经过回火马氏体阶段,逐渐转变为由铁素体(以前称为索氏体)基体中的渗碳体球体组成的组织。这些变化伴随着硬度的降低和韧性的增加。
回火温度取决于所需的性能和钢的使用目的。如果需要足够的硬度,则回火温度要低。另一方面,如果需要足够的韧性,则回火温度要高。淬火钢的适当回火需要一定的时间。在任何选定的回火温度下,硬度起初下降很快,随着时间的延长逐渐下降得更慢。短的回火时间通常是不希望的,应该避免。对于任何淬火钢,良好的做法都需要在回火温度下至少 30 分钟(或者更好是 1 到 2 小时)。
淬火后立即回火的必要性不能过分强调。如果在硬化过程中让完全硬化的钢冷却到室温,则存在钢开裂的危险。碳钢和大多数低合金钢一旦冷却到可以舒适地赤手握持,就需要进行回火处理。钢在冷却到该温度之前不进行回火,因为在某些钢中,Mf 温度非常低并且可能存在未转变的奥氏体。所有这些残余奥氏体的一部分在从回火温度冷却时转变为马氏体,因此更终组织由回火和未回火马氏体组成。脆性未回火马氏体,连同其形成引起的内应力,容易造成热处理钢件失效。当这种情况可能存在时,应进行二次回火处理(双回火),以对初次回火处理后冷却形成的新马氏体进行回火处理。
如果要在正火状态下使用结构钢,正火操作后通常要加热到大约 650 摄氏度到 700 摄氏度的温度。这种处理的目的,也称为回火,是为了减轻内部从正火温度冷却产生的应力和提高钢的延展性。
表面硬化
表面硬化是一种硬化铁合金的过程,使表面层或外壳比内部或核心更硬。在处理过程中,通过添加碳、氮或两者来改变表面层的化学成分。更常用的表面硬化工艺是渗碳、氰化、碳氮化和渗氮。
渗碳– 渗碳是通过将与含碳材料接触的金属加热到高于钢的 A3 温度并保持在该温度的方法,将碳引入固体铁合金的过程。碳的渗透深度取决于温度、在该温度下的时间和渗碳剂的组成。作为粗略的指示,根据渗碳剂的类型,可以是固体、液体或气体,在 930 摄氏度下大约 4 小时可以实现约 0.75 毫米至 1.25 毫米的渗碳深度。由于渗碳的主要目的是获得坚硬的外壳和相对柔软、坚韧的芯部,因此只有低碳钢(更多约 0.25% 的碳),无论是否含有合金元素(镍、铬、锰) ,或钼),通常使用。
渗碳后可以进行各种热处理,但所有这些都涉及对钢进行淬火以硬化渗碳表面层。更简单的处理包括直接从渗碳温度对钢进行淬火。这种处理使表壳和芯都硬化(在芯能够硬化的范围内)。另一种简单的处理,也许是更常用的处理,包括从渗碳温度缓慢冷却,再加热到外壳的 A3 温度(约 775 摄氏度)以上,然后淬火。这种处理只会使外壳变硬。更复杂的处理是双重淬火,包括首先从芯部的 A3 温度以上(低碳钢约 900 摄氏度)淬火,然后从外壳的 A3 温度以上(约 775 摄氏度)淬火。这种处理可以细化核心并硬化表壳。普通碳钢几乎总是在水或盐水中淬火,而合金钢通常在油中淬火。
虽然有时省略渗碳钢淬火后的回火,但在 300 摄氏度左右的低温回火处理是一个很好的做法。有时希望仅对表面的某些部分进行渗碳。这可以通过用一些防止渗碳剂通过的材料覆盖要防止渗碳的表面来实现。更广泛使用的方法是要保护的表面镀铜。还可以使用几种在防止渗碳方面非常有效的专有溶液或糊剂。通常用于填充(固体)渗碳的商业化合物包含碳酸盐(通常是碳酸钡)、焦炭(稀释剂)和硬木炭的混合物,以油、焦油或糖蜜作为粘合剂。烧焦的皮革、骨头和木炭的混合物也被使用。这些化合物的渗碳作用在使用过程中会减弱,因此必须在化合物重新使用之前添加新材料。将一份未使用过的化合物添加到三到五份使用过的化合物中是常见的做法。
要渗碳的零件装在由耐热合金制成的盒子(或其他合适的容器)中,尽管在盒子的长寿命不重要的地方也可以使用轧制钢或铸钢。箱顶盖用耐火粘土或其他耐火材料密封,以防止渗碳温度下产生的渗碳气体逸出。箱子的深度和均匀度受包装方法和容器设计的影响。液体渗碳包括在熔盐浴中对钢或铁进行表面硬化处理,熔盐浴主要含有氰化物(剧毒)、氯化物和碳酸盐的混合物。用这种方法生产的表壳同时含有碳和氮,但主要是前者。使用的温度范围从大约 850 摄氏度到 900 摄氏度或更高,取决于浴液的成分和所需的外壳深度。在 900 摄氏度时,可在 1 小时内实现约 0.25 毫米至 0.4 毫米的表壳深度,在 4 小时内可实现约 0.5 毫米至 0.75 毫米的深度。在更高的温度和更长的时间内可以获得相当深的情况。
渗碳后,钢要像固体渗碳一样淬火,但通常直接从熔池中进行。在当今所有的商业气体渗碳中,结合使用两种或多种碳氢化合物来为钢提供碳。使用的碳氢化合物是甲烷、乙烷、丙烷和油蒸气。钢部件放置在密封容器中,渗碳气体通过该容器循环。使用的温度在 925 摄氏度附近。气体渗碳钢中渗碳层深度的平均预期如图 4 所示。渗碳后,钢要进行淬火硬化。
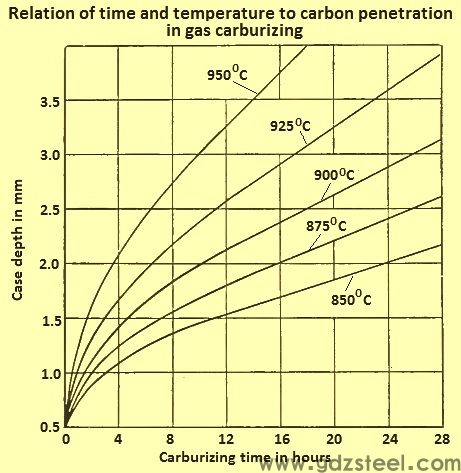
图 4 气体渗碳中时间和温度与渗碳的关系
氰化——通过氰化可以在低碳钢上迅速形成坚硬的表面。这个过程涉及将碳和氮都引入钢的表层。要氰化的钢通常在氰化物-碳酸盐-氯化物盐(通常含有 30% 至 95% 的氰化钠)的熔浴中加热,然后在盐水、水或矿物油中淬火。操作温度一般在 850 摄氏度到 875 摄氏度的范围内。外壳深度是时间、温度和氰化物浴成分的函数。与渗碳相比,浸渍时间相对较短,一般在15分钟到2小时左右不等。更大表壳深度很少超过 0.5 毫米左右,平均深度要小得多。
钢也可以通过加热到适当的温度并浸入粉末状氰化物混合物中或将粉末洒在钢上,然后淬火来进行氰化。这样形成的外壳非常薄。如果让氰化盐接触划痕或伤口,则剧毒。如果内服,它们会致命。当氰化物与酸接触时,会产生致命的有毒烟雾。氰化浴应配备通风罩,用于排放加热过程中产生的气体,工作间应通风良好。绝不允许熔融氰化物与通常用于回火浴的硝酸钠或硝酸钾接触,因为混合物具有爆炸性。此外,在准备盐浴时需要小心,钢在放入熔浴之前要完全干燥。
碳氮共渗——碳氮共渗也称为气体氰化、干氰化和镍碳化。它是一种在气体渗碳气氛中对钢零件进行表面硬化的工艺,该气氛中含有受控百分比的氨。碳氮共渗主要用作氰化的低成本替代品。与氰化过程一样,钢中同时添加了碳和氮。该工艺在钢的 A1 温度以上进行,实际温度可达 925 摄氏度。油中淬火速度足够快,可以达到更大的表面硬度。这种适中的冷却速率趋于使变形更小化。碳和氮的渗透深度随温度和时间而变化。碳的渗透与气体渗碳中的渗透大致相同(图 3)。
渗氮——渗氮工艺包括在 500 摄氏度至 540 摄氏度左右的温度下,使经过机加工和热处理的钢(没有表面脱碳)经受含氮介质(通常是氨气)的作用。非常坚硬的表面是通过这个过程获得。表面硬化效应是由于氮的吸收,因此不需要对钢进行后续热处理。所需时间较长,一般为1天至2天。这种情况,即使经过2天的氮化处理,通常也小于0.5毫米。更高硬度存在于表层,深度仅为百分之几毫米。
已经开发了用于渗氮的特殊低合金钢。这些钢含有容易与氮结合形成氮化物的元素。这些元素中更有利的是铝、铬和钒。这些钢中使用钼和镍来增加强度和韧性。碳含量通常在 0.20% 到 0.50% 左右,尽管在某些需要高核心硬度的钢中,它可以高达 1.3%。不锈钢也可以进行氮化处理。
由于氮化是在较低的温度下进行的,因此使用调质钢作为基材是有利的。这提供了一个坚固、坚韧的核心和一个非常坚硬的耐磨外壳,实际上,它比通过淬火硬化碳化或氰化钢获得的要硬得多。虽然在渗氮过程中翘曲不是问题,但在此处理过程中钢的尺寸略有增加。可以在成品中考虑到这种增长。可以通过镀锡、镀铜或镀青铜,或使用某些涂料来防止氮化。
表面硬化
通常只需要硬化钢的表面而不改变表面层的化学成分。如果钢中含有足够的碳以响应硬化,则可以仅通过非常快速的短时间加热来硬化表面层,从而通过淬火来调节表面以进行硬化。
感应淬火– 在感应淬火中,高频电流通过围绕钢的线圈,其表面层通过电磁感应加热。加热区延伸的深度取决于电流的频率(频率越低,深度越大)和加热循环的持续时间。将表面层加热到 A3 以上温度所需的时间非常短,通常只需几秒钟。通过适当设计线圈或感应器块来实现选择性加热(并因此硬化)。在加热循环结束时,钢通常由穿过感应线圈的水射流淬火。控制操作的**方法,即能量输入速率、加热持续时间和冷却速率,是必要的。
火焰硬化——通过高温火焰将钢的表层加热到转变温度以上然后淬火的过程。在这个过程中,气体火焰直接撞击待硬化的钢材表面。加热速度非常快,虽然没有感应加热那么快。普通碳钢通常通过喷水进行淬火,而合金钢的冷却速度可以根据成分的不同从快速水淬到慢速空冷不等。任何类型的可硬化钢都可以进行火焰硬化。为获得更佳结果,碳含量应至少为 0.35%,通常范围为 0.40% 至 0.50%。
特殊处理工艺
特殊处理工艺通常包括等温淬火、等温淬火和冷处理
Austempering – Austempering 是**热处理工艺的商标名称。基本上,它包括将钢加热到 A3 转变温度以上,然后在低于细珠光体形成温度的热浴中淬火(S 曲线的前端,图 2),但高于 Ms 温度如图3所示。奥氏体在该温度区等温分解产物为贝氏体。该成分结合了相对较高的韧性和硬度。
等温淬火过程具有一定的局限性,使其不适用于许多钢。为了确保均匀的结构(以及因此均匀的性能),钢的整个横截面必须足够快地冷却,以使即使中心在 S 曲线的前端也能逃脱转变。在碳钢中,在 S 曲线前端开始转变所需的时间非常短,因此只有相对较小的部分(更大厚度约为 10 毫米)才能在等温淬火槽中成功地进行热淬火。合金钢的奥氏体转变为细珠光体所需的时间通常较长,因此较大的截面可以成功地等温回火(更大约 25 毫米)。然而,
淬火– Martempering 包括将钢加热到其 A3 转变温度以上,然后在大约等于其 Ms 温度的温度下淬火。将钢保持在热浴中,直到其温度基本均匀,然后在空气中冷却。在硬化过程中,钢中会产生严重的内应力。钢在冷却过程中收缩,但在奥氏体转变为马氏体时发生显着膨胀。由于淬火钢是从表面向内冷却的,因此各个部分在不同的时间发生转变。钢因此受到各种不同的膨胀和收缩,导致相当大的内应力。通过在转变发生之前平衡整个部分的温度,
冷处理– 许多合金钢的 Mf 温度很低,以至于在淬火至室温或回火后冷却时不会发生奥氏体向马氏体的完全转变。这种残余奥氏体可以通过冷却到大气温度以下而部分或完全转变,这种处理称为“冷处理”。冷处理的有益效果尚未得到充分探索。众所周知,高合金钢的残余奥氏体通常难以转变。淬火后立即将这些钢冷却至低温(至固态 CO2 的温度或什至更低)有时可以有效地转变残余奥氏体,但有相关的开裂危险。回火后进行冷处理时,残余奥氏体对转变的抵抗力要大得多。如果使用冷处理,钢总是要在后回火。
反复交替加热至略低于用于回火的温度,并在冷冻的冰盐水中冷却至零下温度,二氧化碳、液态空气或液氮通常用于转变钢量规的残余奥氏体(尺寸稳定),尤其是那些滚珠轴承型组合物。
原文链接:优钢网 » 钢的热处理工艺-时间-温度-转变曲线- 气体渗碳中时间和温度与渗碳的关系
发表评论